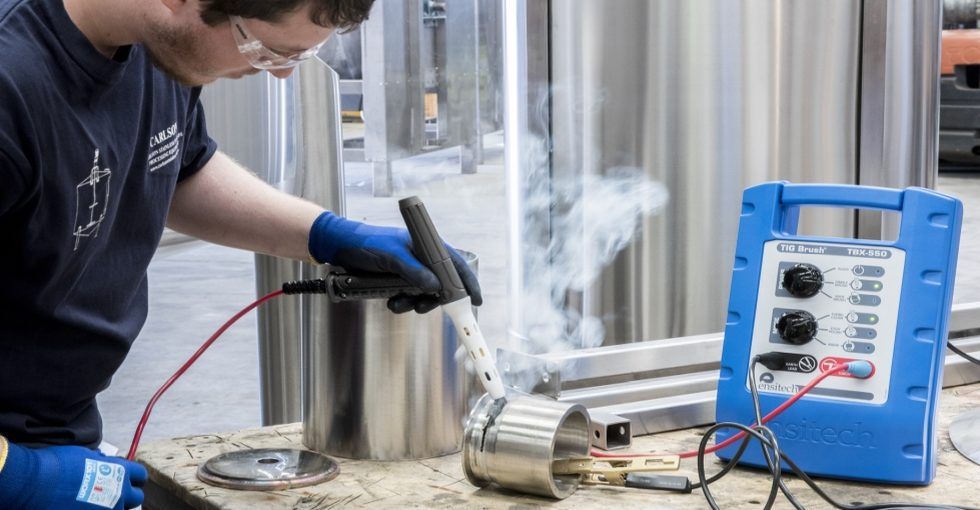
Pasywacja oraz czyszczenie stali nierdzewnej oraz spoin
Stal nierdzewna nie rdzewieje ponieważ posiada na powierzchni warstwę zwaną warstwą pasywną chroniącą ją przed korozją, czynnikami chemicznymi i atmosferycznymi.
Warstwa pasywna jest cienką warstwą tlenku powstałego na powierzchni metalu. Wytwarza się, gdy zachodzi reakcja chemiczna pomiędzy chromem zawartym w stali nierdzewnej (chromowej) a tlenem znajdującym się w powietrzu. W wyniku takiej reakcji powstaje tlenek chromu stanowiący warstwę ochronną dla stali.
Niestety warstwa pasywna na powierzchni stali nierdzewnej nie jest trwała, i może ulec uszkodzeniu. Najczęściej naruszenie takiej powłoki spowodowane jest poprzez:
• spawanie,
• szlifowanie,
• cięcie,
• reakcje chemiczne,
• powstałe zabrudzenia.
Gdy dojdzie do uszkodzenia powłoki pasywnej, np. w skutek spawania – niezbędne jest ponowne wykonanie pasywacji. W przeciwnym wypadku stal straci właściwości nierdzewne i będzie reagowała na czynniki zewnętrzne. Ponowną pasywację należy rozpocząć od dokładnego oczyszczenia danego fragmentu stali, m.in. z cząstek żelaza, usunięcia tlenków zgorzelinowych powstałych podczas przegrzania materiału, odbarwień termicznych po procesie spawania, usunięcia zabrudzeń eksploatacyjnych itd.
Następnie na tak oczyszczonej powierzchni ponowna pasywacja może zostać wykonana poprzez jedną z dwóch metod:
1. użycie specjalnych past trawiących;
2. użycie specjalnego urządzenia do elektrolizy chemicznej;
Pasywacja przy użyciu past chemicznych polega na nałożeniu w pierwszej kolejności past trawiących, które wytrawią (usuną) przebarwienia termiczne, a następnie na nałożeniu specjalnego preparatu chemicznego, opartego na bazie kwasu azotowego, który przywróci warstwę tlenków chromu na powierzchni stali.
Po nałożeniu preparatu chemicznego do pasywacji, proces wytwarzania warstwy pasywnej wynosi ok 24 godzin. Zalety zastosowania past trawiących i pasywujących to z pewnością relatywnie niewielka cena.
Największe minusy stosowania takich past to:
• zawartość kwasu azotowego (niebezpieczne dla środowiska, niebezpieczne dla użytkowników, mogą pozostawiać ślad lub nalot na pasywowanej powierzchni);
• czasochłonne i wymagające dużej dokładności pasywowanie dużych powierzchni metalu;
• długi okres wytwarzania się warstwy pasywnej (ok. 24 godziny po nałożeniu preparatu);
Warto wiedzieć, że w tej metodzie używane są pasty trawiące na bazie kwasów, które mogą podrażniać oczy, skórę czy układ oddechowy. Z tego względu wymagane jest noszenie specjalnej odzieży ochronnej i przeprowadzanie procesów czyszczenia przez osoby do tego uprawnione. Metoda chemiczna ma jeszcze jedną wadę, a mianowicie odpady chemiczne, które należy poddać utylizacji.
Pasywacja przy użyciu urządzeń do elektrolizy chemicznej polega na zastosowaniu specjalnego urządzenia, które dzięki swej konstrukcji wykorzystuje energię elektryczną (prąd), temperaturę i specjalny płyn (elektrolit) do przeprowadzenia procesu elektrochemicznego, którego wynikiem jest powstanie warstwy pasywnej.
Stosując urządzenia do elektrolizy chemicznej równocześnie usuwa się zabrudzenia termiczne powstałe w wyniku spawania i przywraca się warstwę pasywną.
Wady zastosowania urządzeń do elektrolizy chemicznej:
- wyższa cena niż w przypadku klasycznych past chemicznych do pasywacji;
Zalety zastosowania urządzeń do elektrolizy chemicznej:
- bezpieczna dla użytkownika i środowiska;
- jednoczesne czyszczenie zabrudzeń termicznych i pasywacja;
- łatwiejsze i szybsze czyszczenie i pasywowanie powierzchni;
- natychmiastowe powstawanie warstwy pasywnej;
TIG Brush jest nowoczesnym zaawansowanym urządzeniem do czyszczenia, polerowania, pasywacji i znakowania stali nierdzewnej. Urządzenia wykorzystują metodę elektrochemiczną stosując prąd, temperaturę i odpowiednie elektrolity. Zastosowany w urządzeniach specjalny uchwyt PROPEL, odporny jest na wysoką temperaturę i przewodzenie prądu.
Ponadto uchwyt umożliwia w łatwy i wygodny sposób trzymanie szczotki z naniesionym elektrolitem, regulację długości szczotki, możliwość regulacji szerokości czyszczonej powierzchni (1-4 szczotki na szerokość), dzięki czemu możliwe jest łatwiejsze i szybsze czyszczenie i pasywacja.
Urządzenie TIG-550 usuwa przebarwienia powstałe przy spawaniu metodami TIG, MIG, MAG. Jest to model o większej mocy od TBE-440, dzięki czemu działanie jest jeszcze szybsze.
Urządzenie TBE-700 jest najszybszym urządzeniem tego typu w branży. Zapewnia czyszczenie spoin metodami MIG i TIG z szybkością co najmniej dwukrotnie większą od najbardziej zbliżonego funkcjonalnie konkurencyjnego rozwiązania.
Do powyższych urządzeń oferowane są płyny chemiczne i elektrolity:
• TB-21ND – wysokowydajny i bezpieczny (nie sklasyfikowano działania żrącego) płyn do czyszczenia, polerowania i pasywacji stali nierdzewnej. Jest nieszkodliwy, jego kod NSF: 150090, kod kategorii NSF: A3
• TB-25 – najsilniejszy i najszybciej działający płyn do czyszczenia, polerowania i pasywacji stali nierdzewnej. Sklasyfikowany jako niebezpieczny, jego kod NSF: 150001, kod kategorii NSF: A3
• TB-30ND – ulegający biodegradacji płyn do czyszczenia i pasywacji stali nierdzewnej. Przeznaczony do branż w których niedozwolone jest stosowanie chemikaliów (branża spożywcza/farmaceutyczna). Jest nieszkodliwy, jego kod NSF: 150056, kod kategorii NSF: A3
• TB-31ND – płyn o odczynie PH neutralnym, do czyszczenia i pasywacji stali nierdzewnej. Przeznaczony do wrażliwych środowisk jak np. branża spożywcza/farmaceutyczna/petrochemiczna). Jest nieszkodliwy, jego kod NSF: 150057, kod kategorii NSF: A3
Dzięki eliminacji past trawiących i mniej wydajnych metod czyszczenia proces elektrochemiczny TIG Brush jest preferowaną technologią czyszczenia spoin stali nierdzewnej w firmach, które dbają o jakość i bezpieczeństwo, od przemysłu spożywczego przez budownictwo, instalacje uzdatniania wody, przemysł chemiczny, górniczy, naftowo-gazowy, morski i okrętowy po przemysł energetyczny i jądrowy.