III Ogólnopolska Konferencja Menadżerów Jakości, Produkcji i Logistyki zgromadziła w dniach 18-19 maja w Wieliczce kilkudziesięciu przedstawicieli firm z wielu branż przemysłu. Mogli oni nie tylko poznać najciekawsze – i najbardziej efektywne – metody zarządzania, ale również praktyczne sposoby wdrażania ich w życie. Dzięki nim każde przedsiębiorstwo może stać się z jednej strony inteligentne w swoim działaniu, ale i zarazem innowacyjne technologiczne w swojej ofercie.
Lean w erze digitalizacji
W trakcie konferencji poznać można było podstawowe zasady, związane z inteligentnym przedsiębiorstwem i organizacją uczącą, z najlepszego pod tym względem źródła. Stało się tak za sprawą Mikiharu Aoki, współtwórcy systemu produkcyjnego Toyoty, który jest stałym gościem organizowanego przez Langas Group i Polski Przemysł wydarzenia. – Inteligentne przedsiębiorstwo jest integralnie związane z umiejętnością rozwiązywania problemów. Jest tak dlatego, że sam system i jego organizacja wymusza to, że pracownicy w trakcie wykonywania swoich zadań uczą się wykonywanego przez siebie procesu produkcyjnego, i jednocześnie bezpośrednio przekładają swoją pracę na wykonywanie usprawnień w nim. Ma to wpływ zarówno na większe zyski dla firmy, jak i na ewaluację i wysokość premii dla pracowników – mówi Mikiharu Aoki.
Ciekawym punktem III Ogólnopolskiej Konferencji Menadżerów Jakości, Produkcji i Logistyki stało się z pewnością bezpośrednie zestawienie wywodzącego się z Toyoty i opartego na bezpośrednim udziale pracowników w rozwoju firmy modelu zarządzania z ideą Przemysłu 4.0, który jest obecnie podstawowym elementem kolejnej rewolucji technologicznej, mającej miejsce w przemyśle. Tym bardziej, że ma one swoje źródła w niemieckim modelu zarządzania produkcją. – Industry 4.0 jest odpowiedzią na spersonalizowaną potrzebę konsumenta w nowych warunkach technicznych, jakie przemysł oferuje. Jest to rozwiązanie organizacyjne i techniczne mające na celu zwiększenie efektywności i elastyczności produkcji przy jednoczesnym zachowaniu personalizacji produktu w masowym wytwarzaniu – stwierdza Karol Staworko, dyrektor pionu DF, Motion Control, Siemens. – Każdy z nas jest użytkownikiem smartfona. Jednym z wyznaczników Industry 4.0 jest szybkość dostępu do informacji. Gdy mówimy o coraz większej obróbce danych, to ciekawostka – w ostatnim roku na świecie dane, które zostały zebrane, stanowią ponad 50% wszystkich zapamiętanych danych na świecie, jakie kiedykolwiek zapisano. Tylko 0,5% tych danych zostało w jakiś sposób obrobione jako wartość dodana dla przedsiębiorców. Fakt ten przekłada się na finalny efekt w postaci produktu. Dlatego też dostęp do informacji, a więc forma i wprowadzenie modelu biznesowego związanego z nim, będzie rewolucją. Nazywamy to re-industrializacją, czyli czwartą rewolucją przemysłową. Jest to dla nas dużym wyzwaniem, którego sami się uczymy. Ale chcemy też wspólnie z partnerami biznesowymi wdrażać te rozwiązania u naszych klientów.
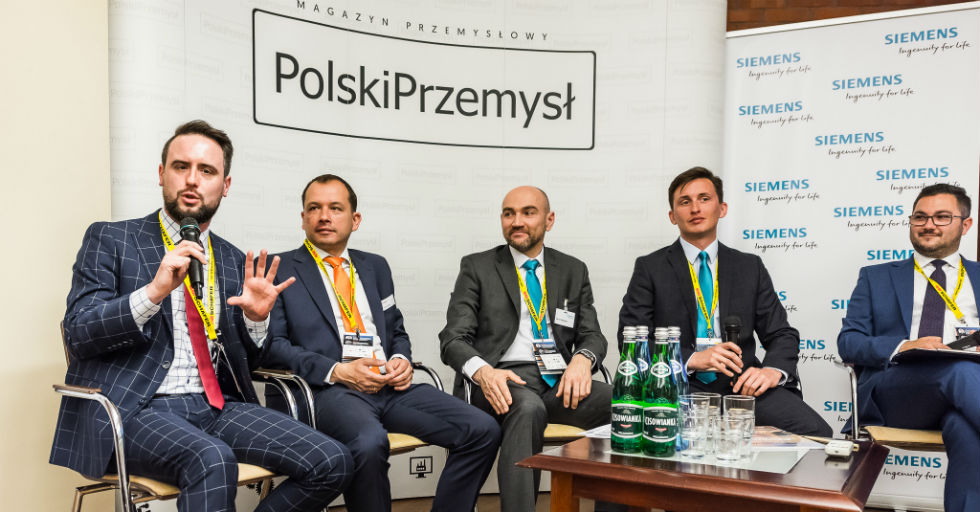
Fot. Impact Photo
Podstawowym wyznacznikiem jest w tym kontekście wspólny projekt koncernów Siemens i Kuka, które wraz z partnerami (Atos, Blumenbecker, Mazak, GM System, KS Automotive oraz SCHUNK Intec sp. z o.o.) zaprezentują w trakcie czerwcowych targów ITM Polska MACH-TOOL kompleksowy, elastyczny system wytwarzania uzupełniony o MindSphere – Siemens Cloud for Industry. W związku z tym ideę Przemysłu 4.0, w trakcie Konferencji w Wieliczce prezentowali: Karol Staworko, a także Robert Chmielewski (konsultant wsparcia sprzedaży w Siemens PLM), Jakub Malicki (Consulting Manager, Atos Polska) i Tomasz Nowak (dyrektor Kuka Polska). Jak widać dzięki najbardziej nowoczesnym technologiom różnego rodzaju podmioty mogą skutecznie współpracować, tworząc sprawnie działający łańcuch dostaw.
Co na to praktyka?
W trakcie pierwszego dnia wydarzenia oryginalne i przede wszystkim skuteczne rozwiązania w zakresie zarządzania współczesnymi zakładami przemysłowymi, zobaczyć można było na przykładzie prezentacji m.in. Krzysztofa Fieglera – współtwórcy i członka zarządu UIBS Teamwork (przedstawił on IPOsystem, będący inteligentnym systemem zarządzania produkcją), a także Adama Batora dyrektora zarządzającego SOLIDEXPERT, Jakuba Wiki – Logistic Consultanta Business Development Automation w firmie SSI SCHAFER POLSKA, Tomasza Szlązaka wiceprezesa Radomskiego Centrum Innowacji i Technologii z firmy Infinitech 3D, a także Artura Sadzika – Kierownika ds. Projektów Strategicznych Transition Technologies S.A.
W związku z tym istotnym punktem odniesienia Konferencji był jej praktyczny wymiar. Dlatego też ważne stały się w jej trakcie nie tylko modele zarządzania współczesnym przemysłem, ale przede wszystkim ich bezpośrednie wdrożenia w konkretnych rozwiązaniach na poszczególnych etapach produkcji. Przykładem tego była dyskusja, która miała miejsce podczas prezentacji Michała Wolaka, eksperta ds. Lean Management, Lean Action sp. z o.o. Jak stwierdził prelegent: – Moje doświadczenie jest takie, że z pracowników liniowych łatwo przekonać do zmiany. Trzeba im pokazać korzyści, jakie będą dzięki temu mieli. Większy problem jest z brygadzistami i kierownikami. Często podchodzą oni do zmian negatywnie, gdyż wychodzą z założenia, że są źle oceniani – argumentuje Michał Wolak. – Za to z prezesami firm wdrażanie zmian jest łatwe. Trzeba im tylko pokazać korzyści finansowe, które wynikają z wdrożenia. Najtrudniej jest z pracownikami na stanowiskach kierowniczych. Do nich należy dotrzeć.
To stwierdzenie wywołało interesujący komentarz jednego z uczestników spotkania: – W przypadku magazynów automatycznych również często mamy do czynienia z oporem pracowników, którzy będą na nowych rozwiązaniach pracować. Z naszego doświadczenia wynika, że warto ich zaangażować do planowania pracy danego magazynu, i implementowanego rozwiązania. Pracownicy wtedy czują, że biorą w procesie wdrażania udział, są ważni. Bo tak naprawdę to oni będą na tym nowym rozwiązaniu pracować. Nie możemy mieć podejścia, że my wymyślimy wam magazyn – musimy to zrobić razem. Im więcej ludzi po stronie klienta jest w ten proces zaangażowanych, tym łatwiej jest potem te zmiany wprowadzać i zachęcić pracowników, by na tym rozwiązaniu pracowali. Ważne jest uświadomienie im tego, że robimy to nie po to, żeby zoptymalizować liczbę pracowników, czyli część zwolnić, ale robimy to po to, żeby firma z tą samą liczbą doświadczonych pracowników mogła rosnąć i rozwijać się.
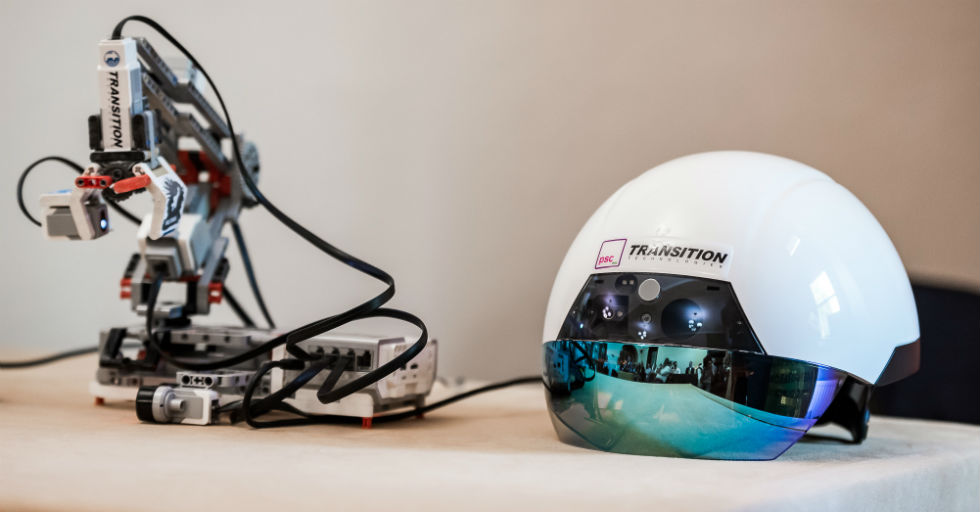
Fot. Impact Photo
Dobre praktyki w tym względzie uczestnicy Konferencji poznać mogli drugiego dnia wydarzenia. Wtedy to miała miejsce analiza procesów logistyki i magazynowania bezpośrednio w zakładzie Medicare w Mysłowicach. Firma m.in. jako pierwsza hurtownia magazynowa w Polsce wprowadziła u siebie system zarządzania jakością, zgodny z normami ISO 9001. Jego efektywność poparta jest corocznymi audytami, przeprowadzanymi przez TUV Nord Polska. Dzięki tej wizycie uczestniczący w spotkaniu w Wieliczce managerowie polskiego przemysłu porównać mogli prezentacje, mówiące o wdrażaniu zmian w swoich spółkach, z konkretnymi rozwiązaniami, realizowanymi w łańcuchu dostaw.
Jaki model zwycięży?
Podstawowe znaczenie – jak wynika z III Ogólnopolskiej Konferencji Menadżerów Jakości, Produkcji i Logistyki – ma to, w jaki sposób wprowadzać zmiany w zarządzaniu firm przemysłowych w czasie trwającej obecnie rewolucji technologicznej. Tak, aby nie tylko umożliwiały one nadążanie za postępem technicznym, ale również (a raczej przede wszystkim) dawały szansę pracownikom na rozwój i uczestniczenie w tym ciągłym procesie zmian, z którym mamy obecnie do czynienia. – Z jednej strony wielkie wrażenie robią na mnie możliwości jakie współcześnie posiadają zakłady produkcyjne, związane z wdrażaniem rozwiązań informatycznych, sztuczną inteligencją itd. Uważam jednak, że warunkiem do tego, by te narzędzia przynosiły rzeczywisty efekt jest to, by one nie były wdrażane w przedsiębiorstwach w stanie obecnym, lecz na znacznie bardziej zaawansowanym poziomie organizacji niż obecnie obserwuję. Dlatego też z mojego punktu widzenia idealne byłoby to, by firmy oferujące najnowocześniejsze rozwiązania informatyczne równocześnie doradzały, co trzeba zrobić, jak trzeba zmienić organizację produkcji. Tak, by te bardzo dobre i zaawansowane narzędzia informatyczne przynosiły dobry efekt. A równocześnie żeby nie zabijały a wzmacniały kulturę kaizen w przedsiębiorstwie – podkreśla Mikiharu Aoki. Japoński specjalista podsumował także potencjalne znaczenie Konferencji w Wieliczce: – To jest znakomity pomysł, że poznajemy dobre rozwiązania i naśladujemy je. Mam nadzieję, że poznawanie tych rozwiązań jest dla Państwa szansą, by je od siebie zapożyczać. Tym bardziej że dla mnie dużą motywacją jest, gdy słyszę, co Państwo robią. Również to inspiruje mnie do dalszej pracy.
Większa fotorelacja z wydarzenia na naszym profilu FB: www.facebook.com/pg/polskiprzemysl/photos